November 2023 Update
28th November, 2023
The main beams needed holes drilling for fixing each of the eighteen rows of ribs, a total of three hundred and seventy-eight (378) holes were required in the beams. Firstly, I made a drilling rig so that each of the beams could be accurately positioned and held in place whilst the holes were marked out then drilled. The drilling rig was made with a sheet of 18mm MDF.
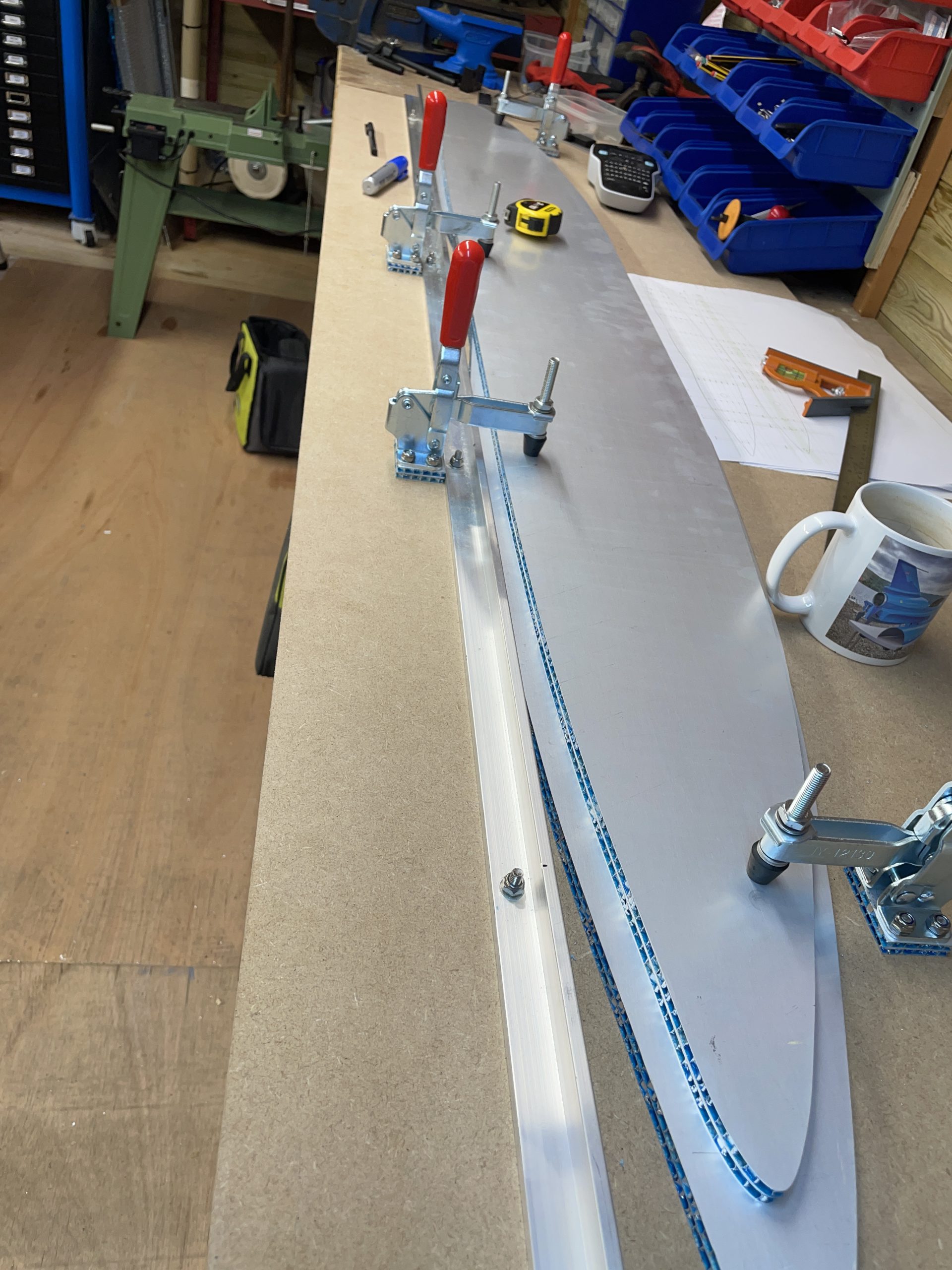
A 25mm x 25mm x 6.4mm aluminium angle was attached to the building frame to form a datum so that accurate measurements could be taken from this point to position the holes accurately on each of the beams. Once all four beams were clamped to the frame the holes which were common to both the main beams and sub-beams (a total of twenty-six holes) could be marked out and drilled. Blue was applied to the surface of the aluminium where required the position of each hole was scribed. The holes were then centre punched with an optical centre punch, centre drilled and finally the clearance holes for the M4 bolts which attach the ribs were drilled.
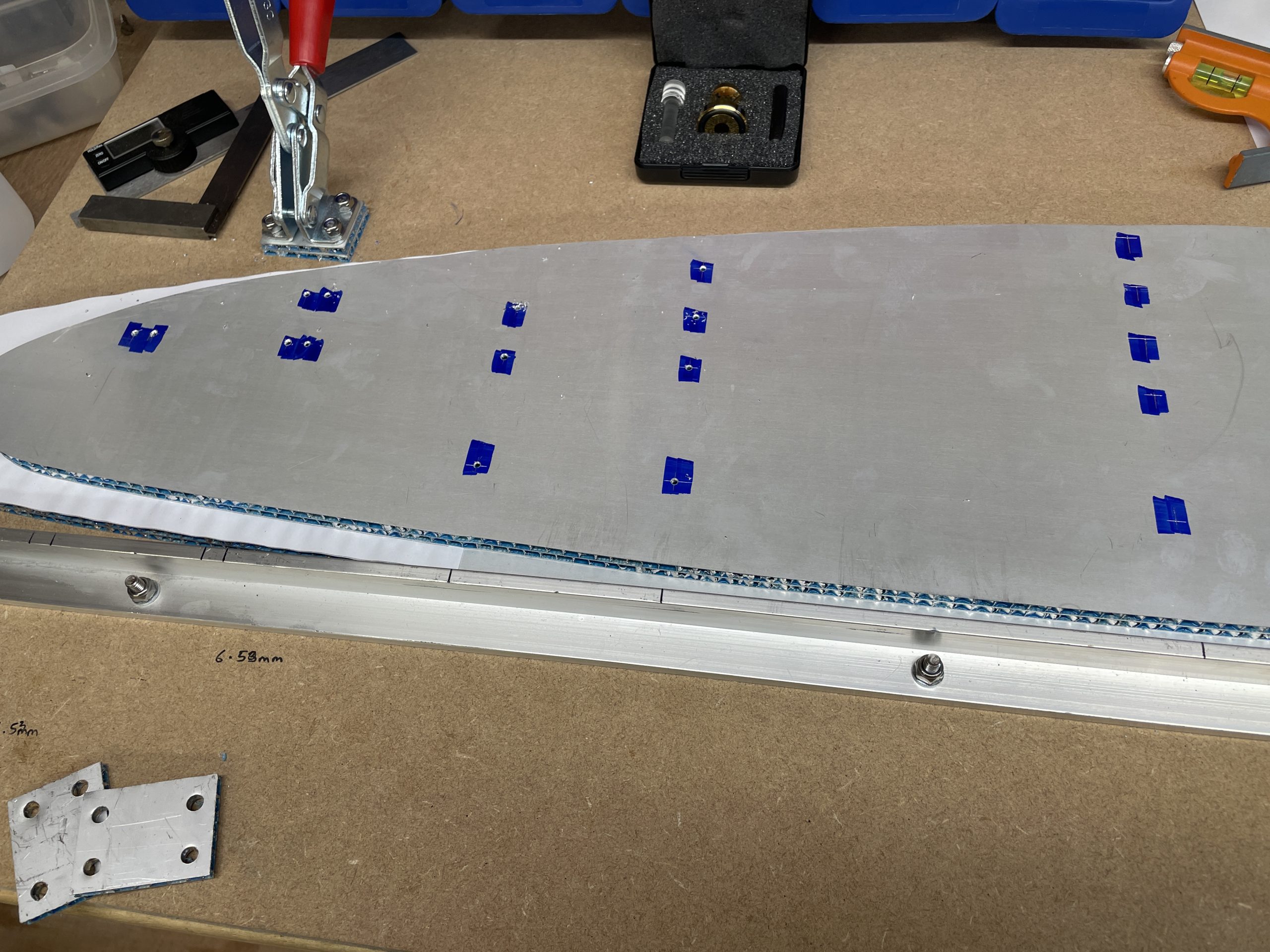
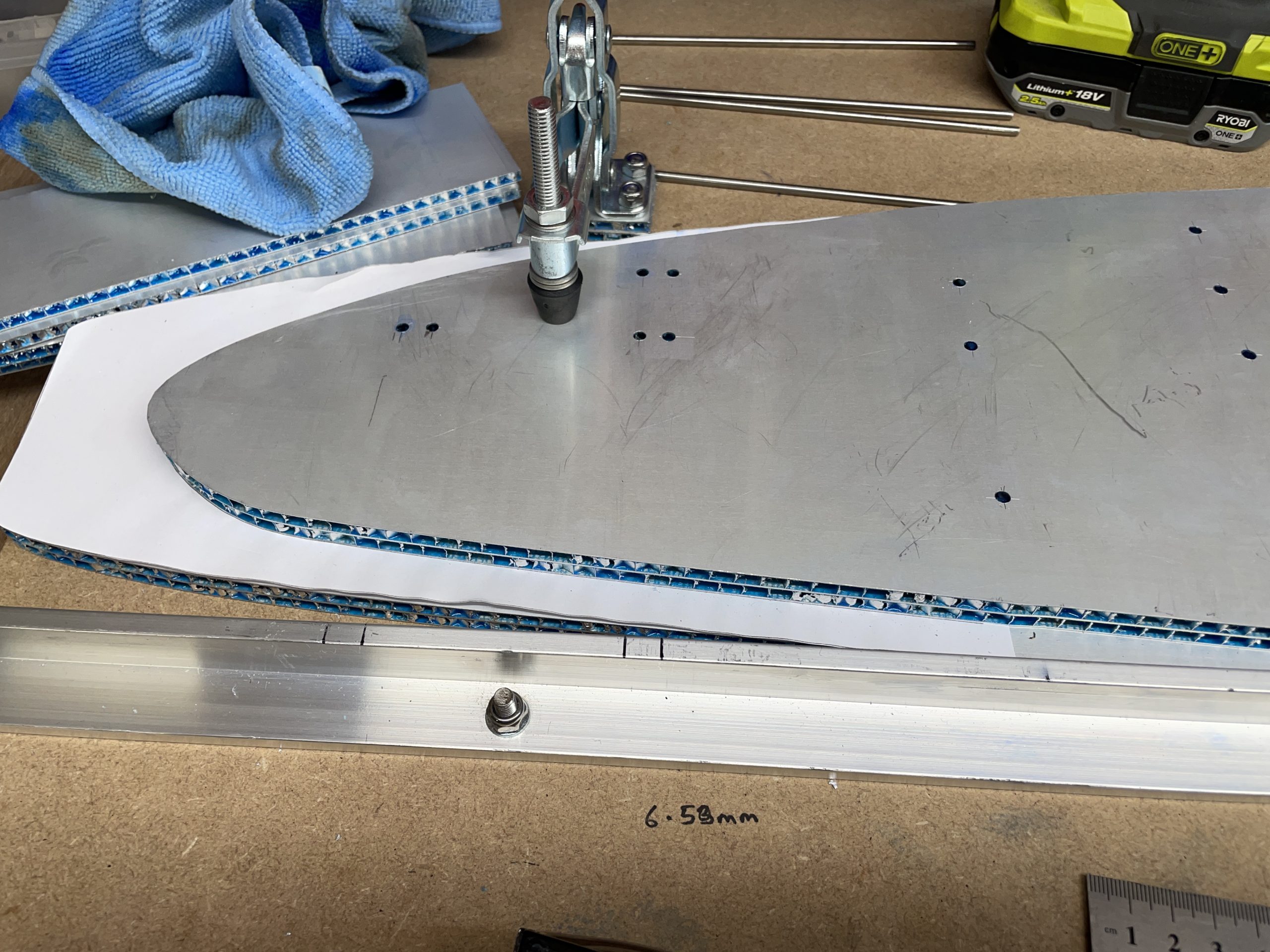
The holes which were common to the main beams and the sub-beams were drilled then the whole assembly was removed from the building frame. The main beams were located back in position with locating pins used to align into the previously drilled holes, then the remainder of the holes in the main beams could be marked out and drilled using the same process as before.
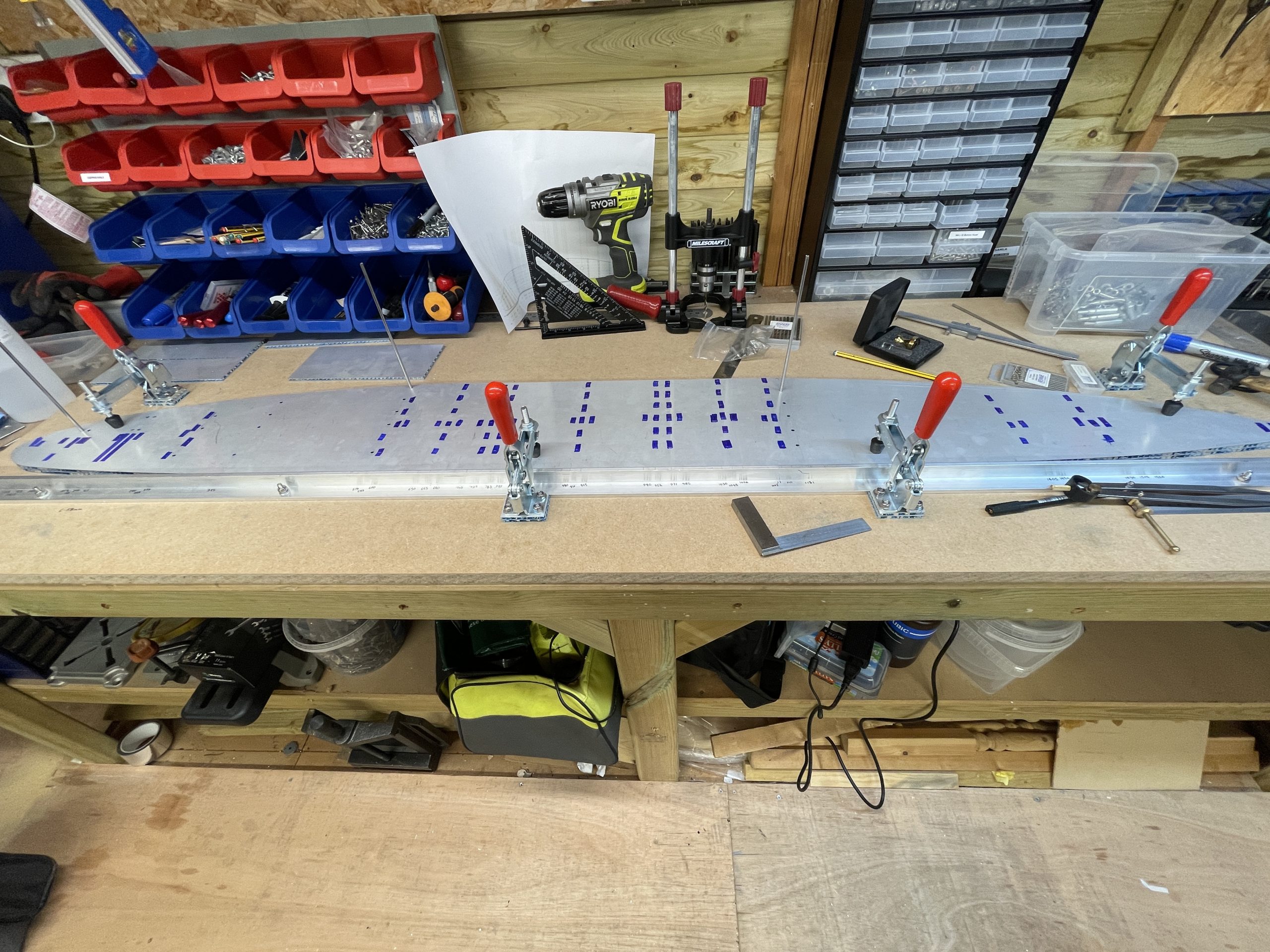
Once all the holes were drilled the main beams drilled and were cleaned up, these could be removed from the building frame. The sub-beams needed to be cut into two pieces and have the centre section removed prior to drilling as the sub-beams do not run the full length of CN7 but fold out to the main beams as can be seen in the image below.
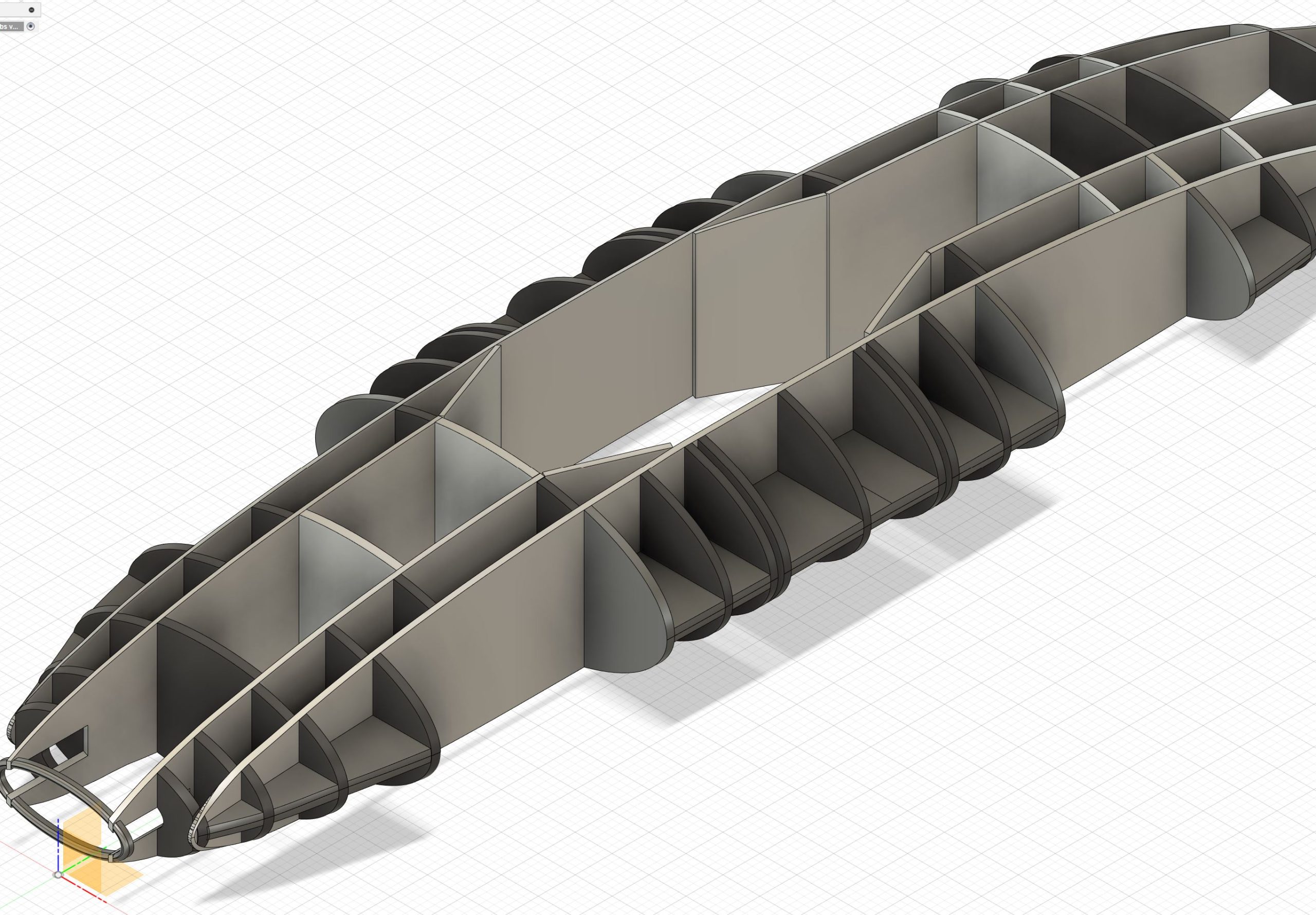
Locating pins were again used to ensure that the holes drilled in the sub-beams would line up correctly with the main beams.
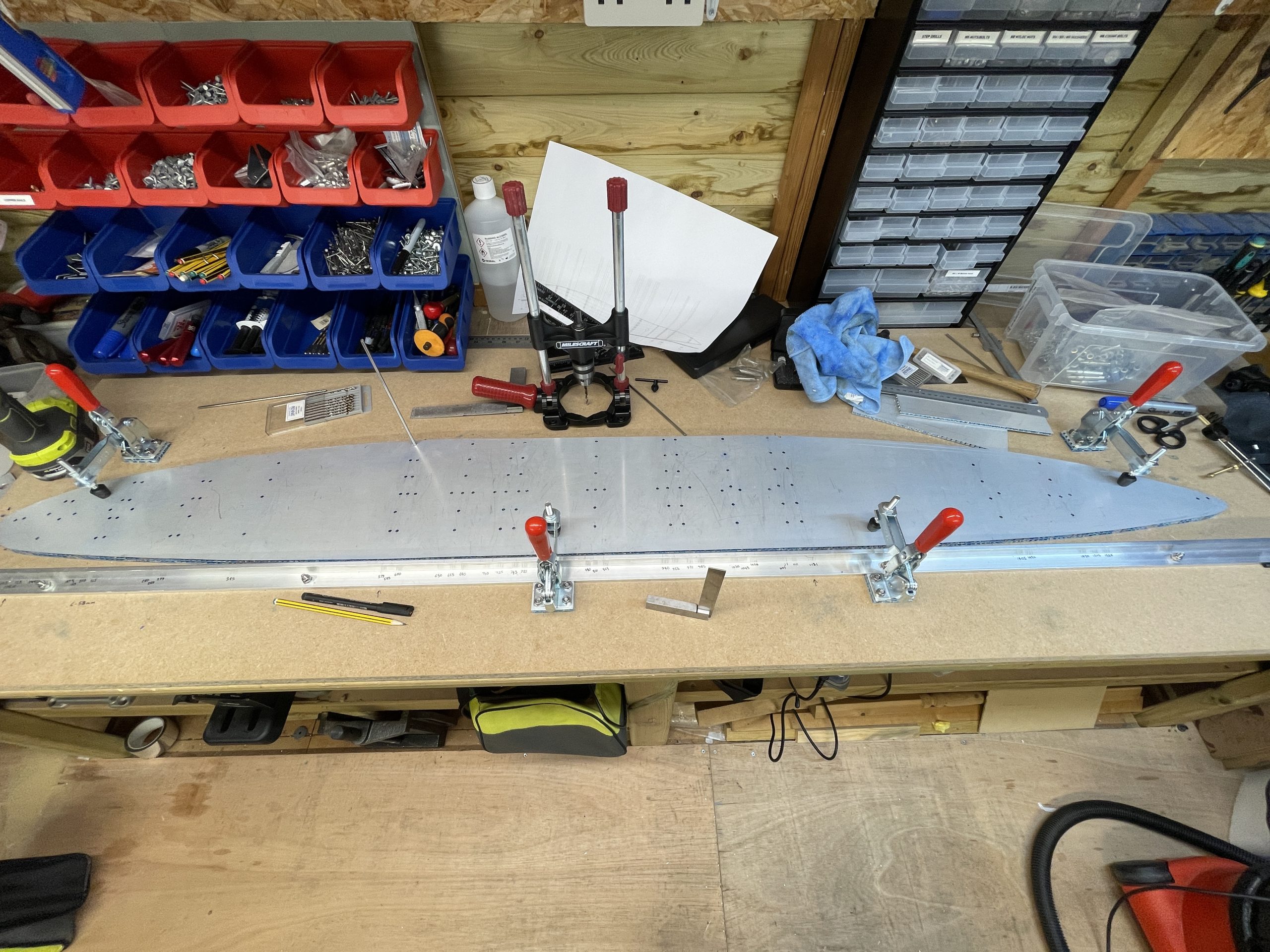
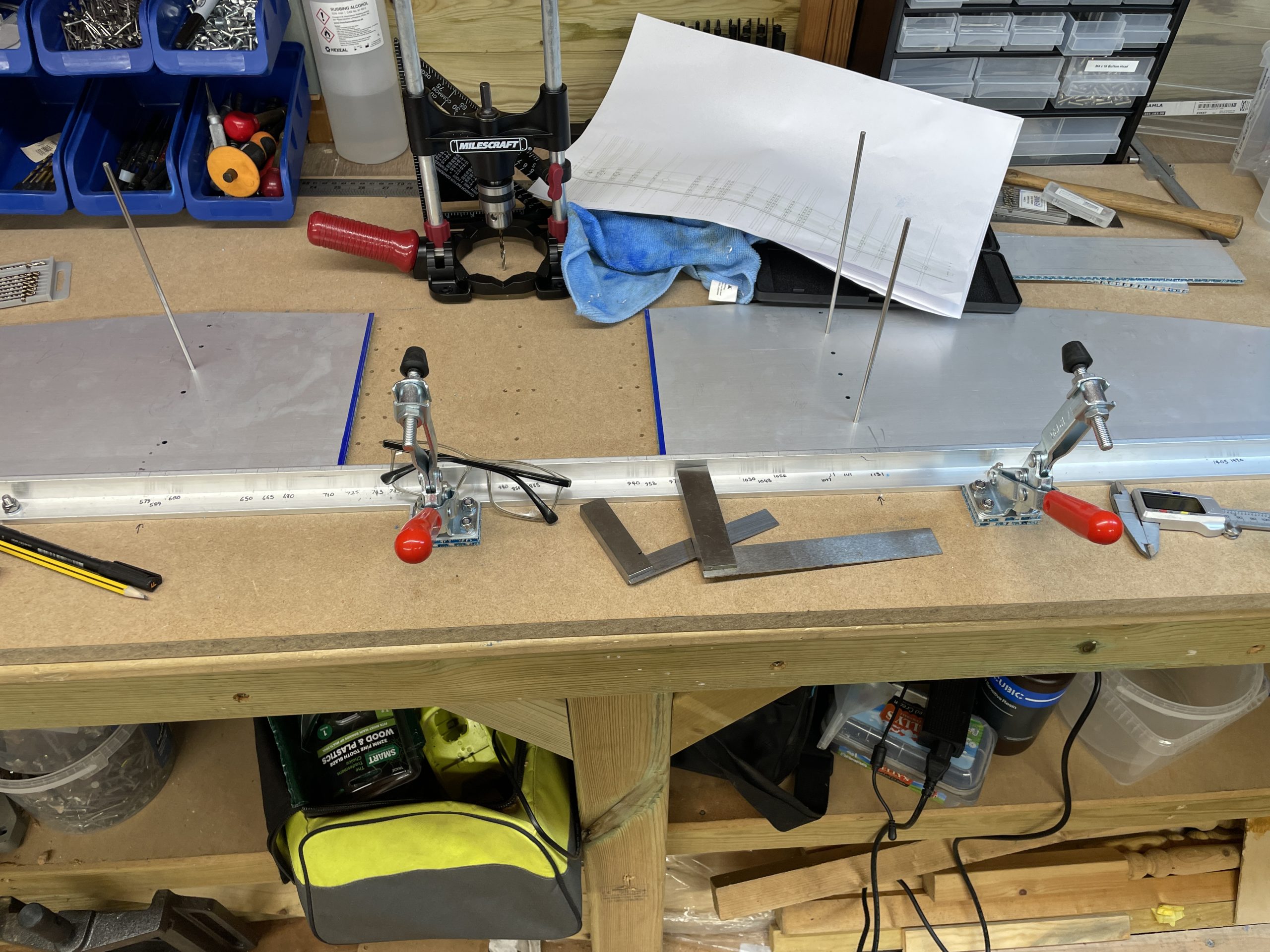
The remaining holes were marked out and drilled into sub-beams.
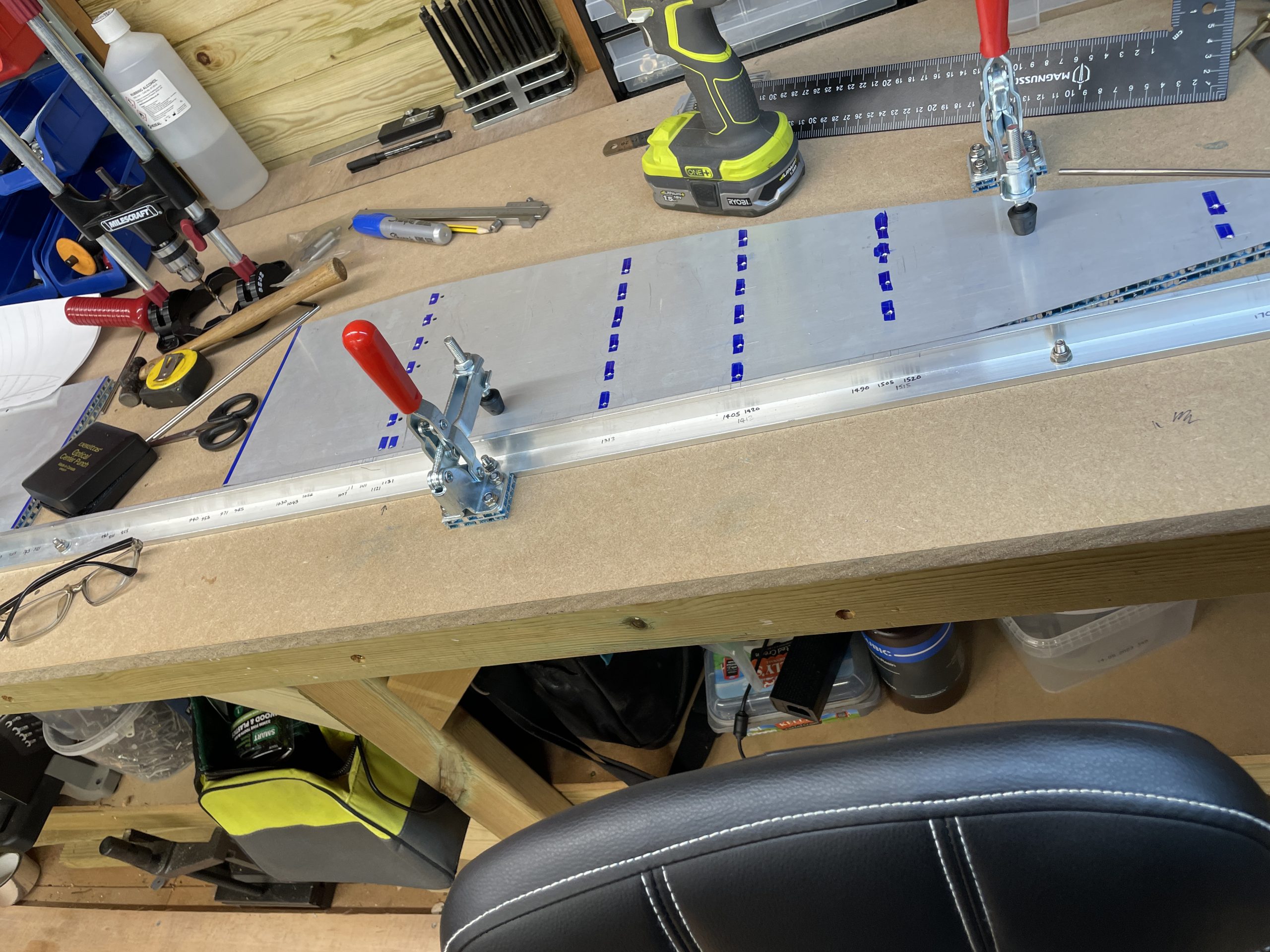
The build can now progress on the main building frame and each of the ribs can be attached to the beams to form the main chassis of CN7. Once fully assembled the beams can marked out and trimmed to fit the profile of each of the ribs to form a fully profiled chassis.
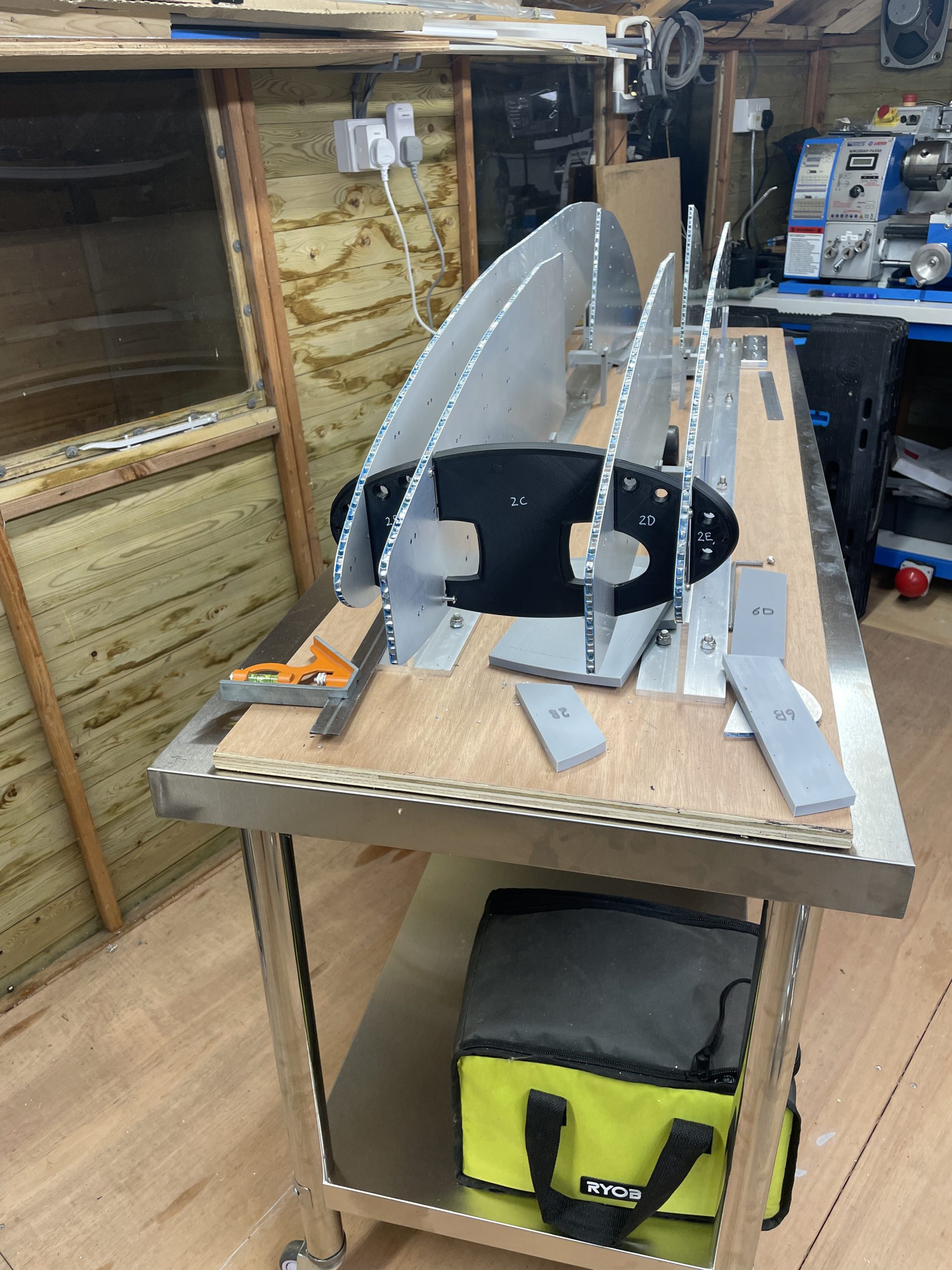
A total of sixty-four rib components are required to complete the full chassis, each component is 3D printed then holes are tapped to accept M4 button head screws. The ones shown below have cut-outs for the air intake tubing and routing of drive shafts and other cabling / pipework.
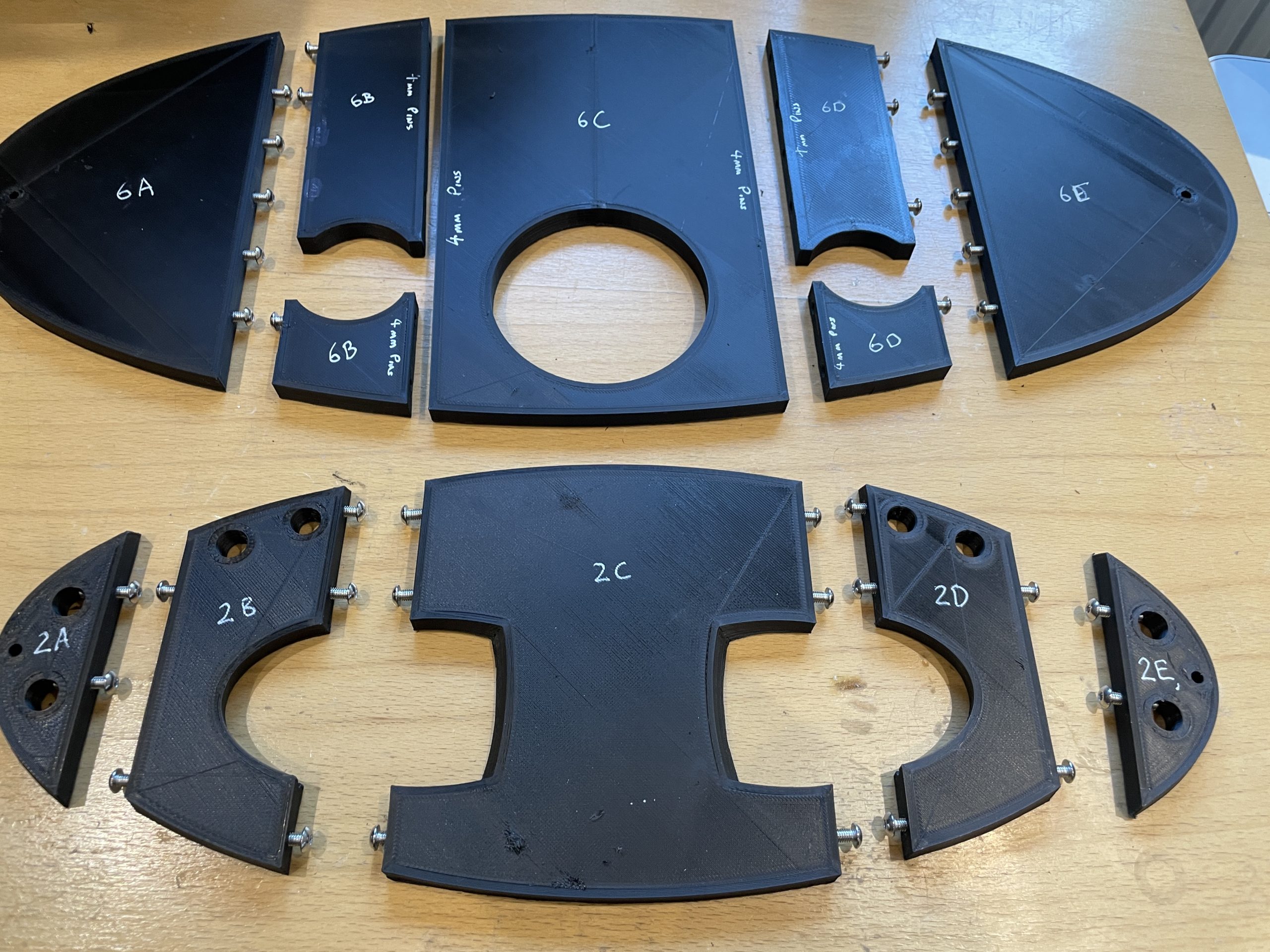
Unfortunately, progress is currently on hold due to an issue with my 3D printer which is preventing any further production of ribs. Whilst trying to change the print nozzle I managed to shear this off in the print head. I am currently waiting for a replacement print head (hot-end) which ships from China therefore I may have a wait until I can continue with the build.
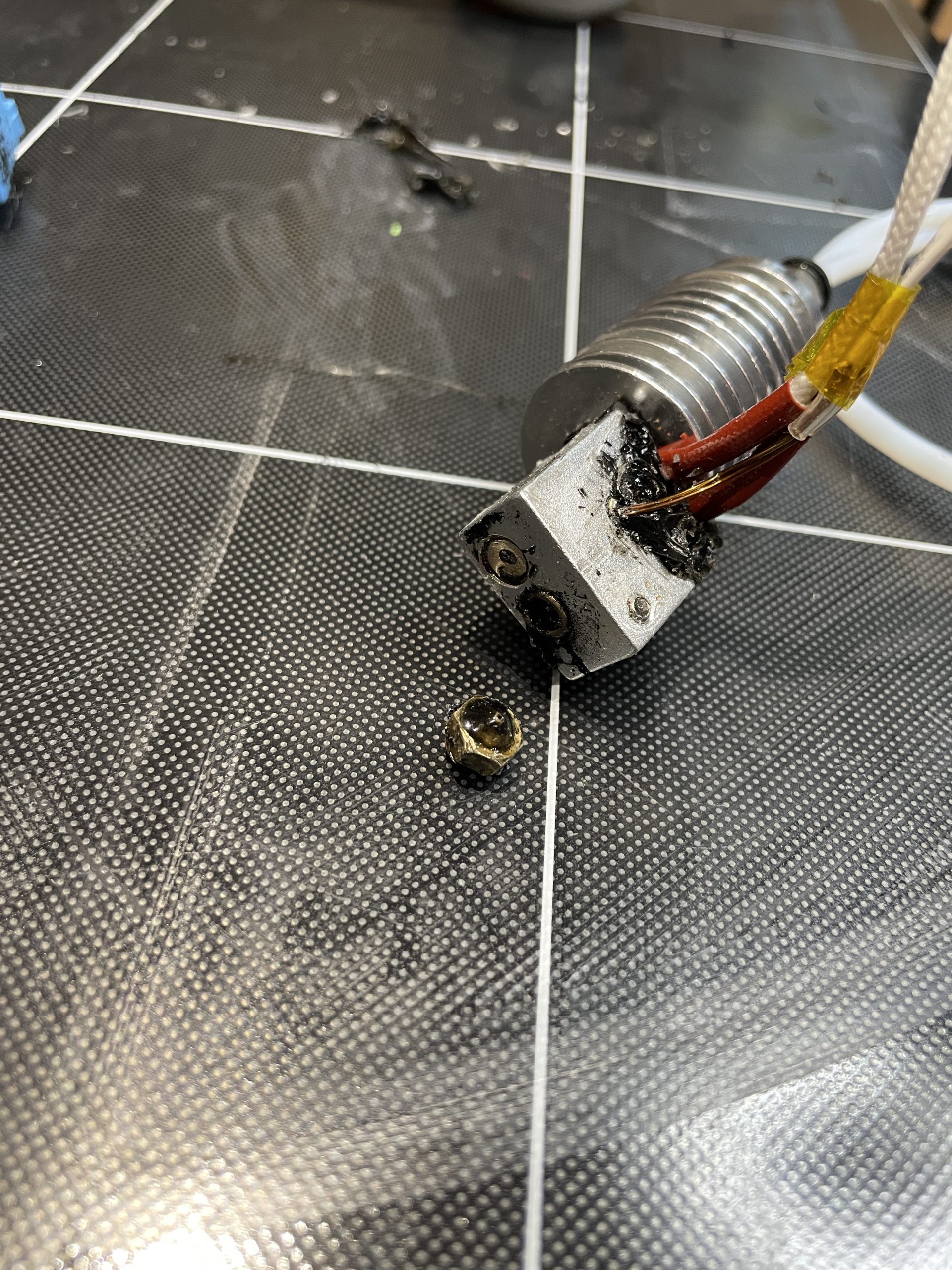