September 2023 Update
30th September, 2023
We started September off with a visit to Coniston, staying at the Coniston Inn, on the shore of Coniston Water, not too far away from Pier Cottage, where Donald Campbell launched his ill-fated run on 4th January 1967.
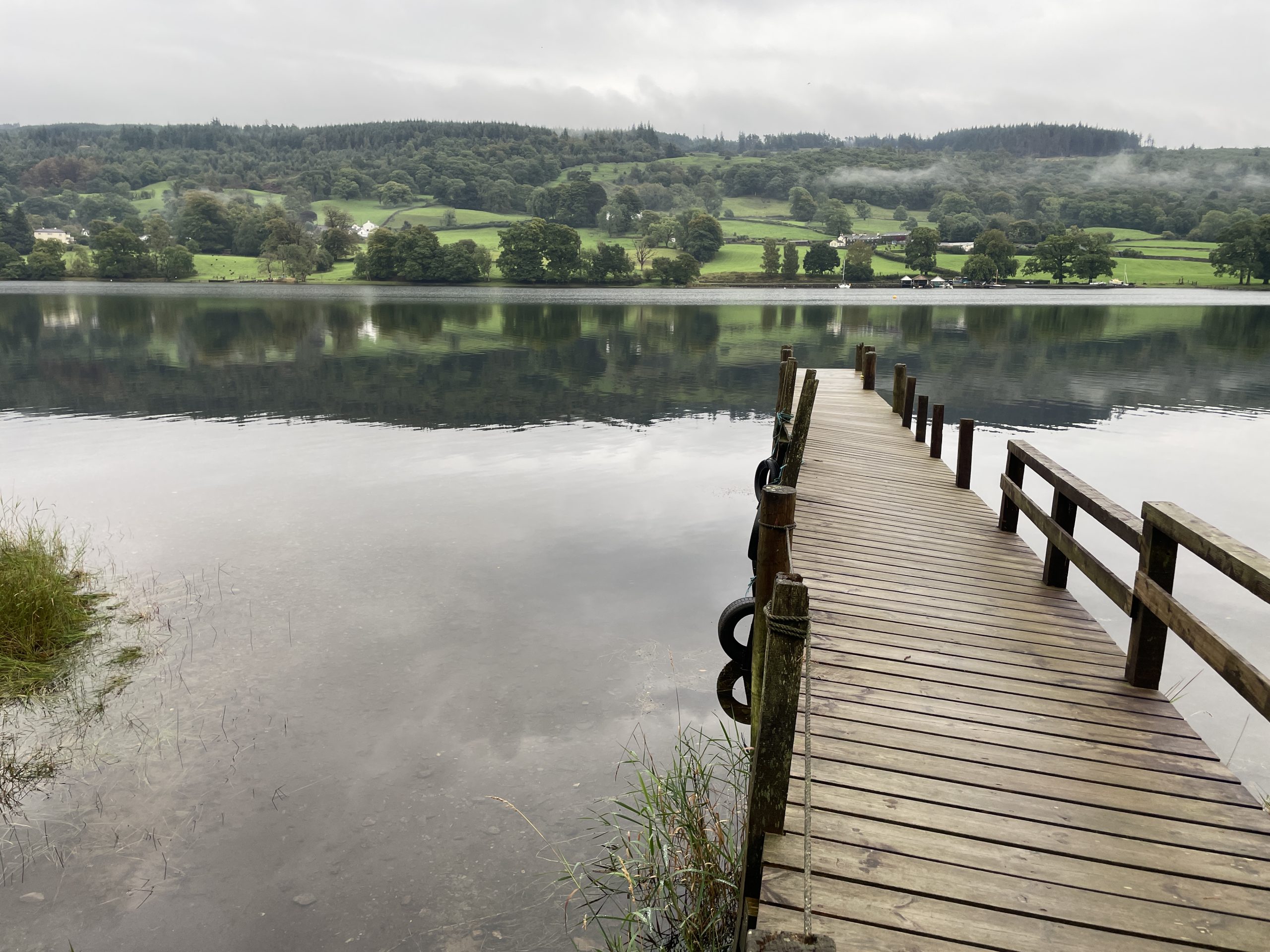
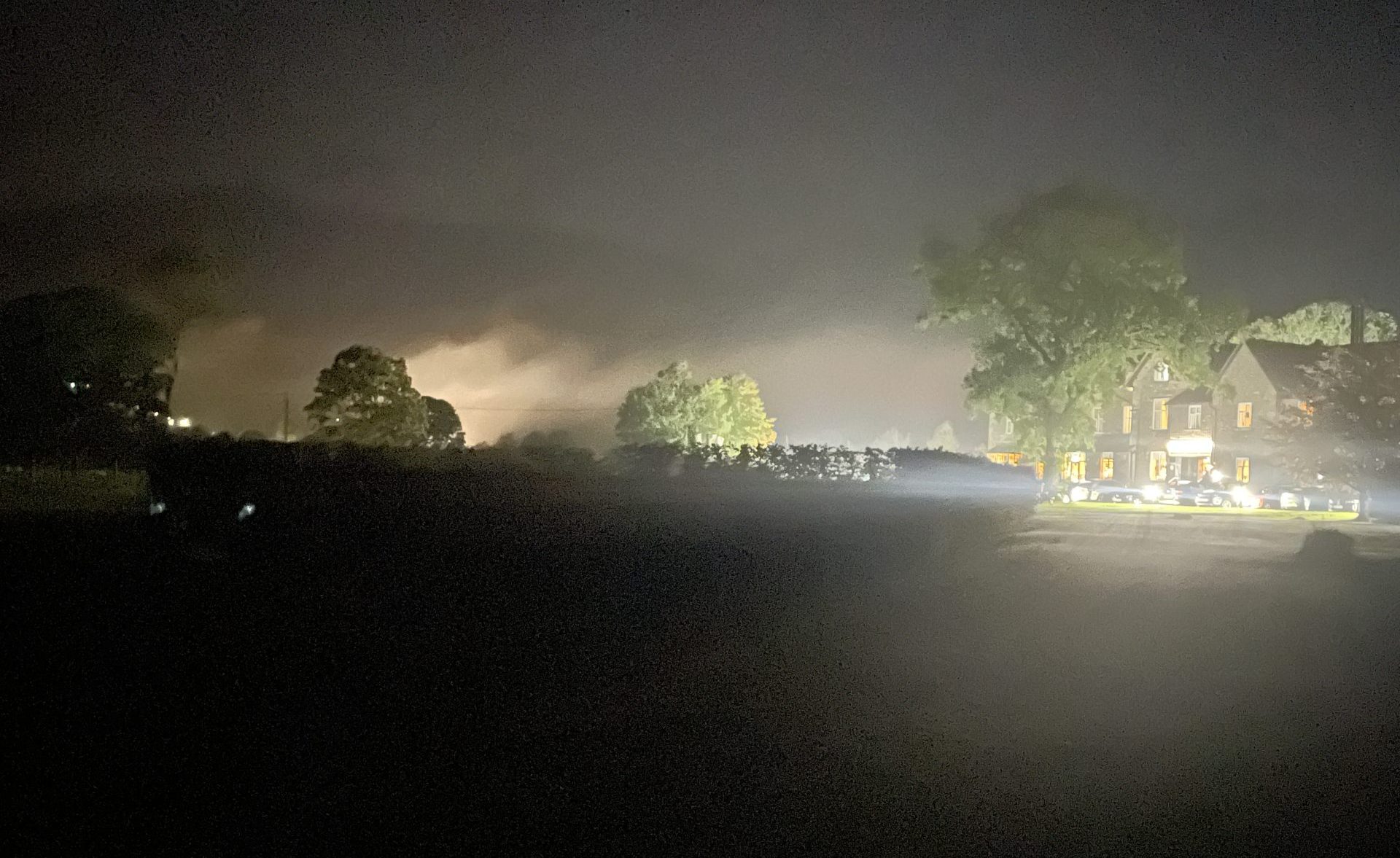
We also visited the grave of the man that started all of this, Donald Campbell and paid our respects. He was finally laid to rest in Coniston Graveyard on 12th September 2001, when his body was recovered by divers from the Bluebird Project.
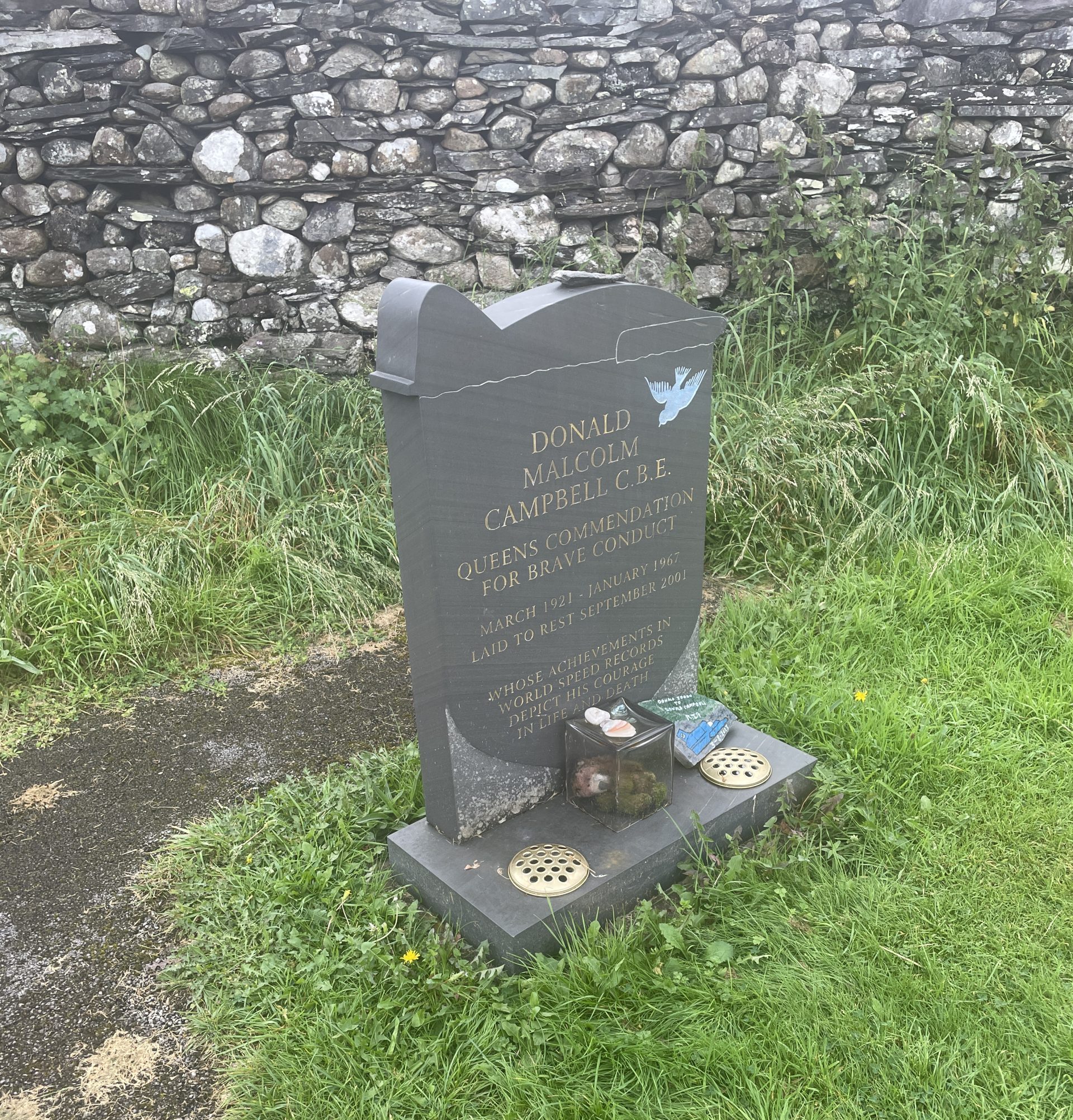
While in Coniston, I visited the Ruskin Museum to pick up my previous project, the 1:5 scale model of Bluebird K7 which has been on display in the Bluebird Wing at the museum over the summer alongside the space that is reserved for the recovered and now restored original Bluebird K7.
After test runs at the 2022 Ruskin Museum model boat regatta my model of Bluebird K7 now requires some alterations to improve water flow around the sponsons. To return to next year’s model boat regatta in the hope of setting a new speed record for jet powered model boats.
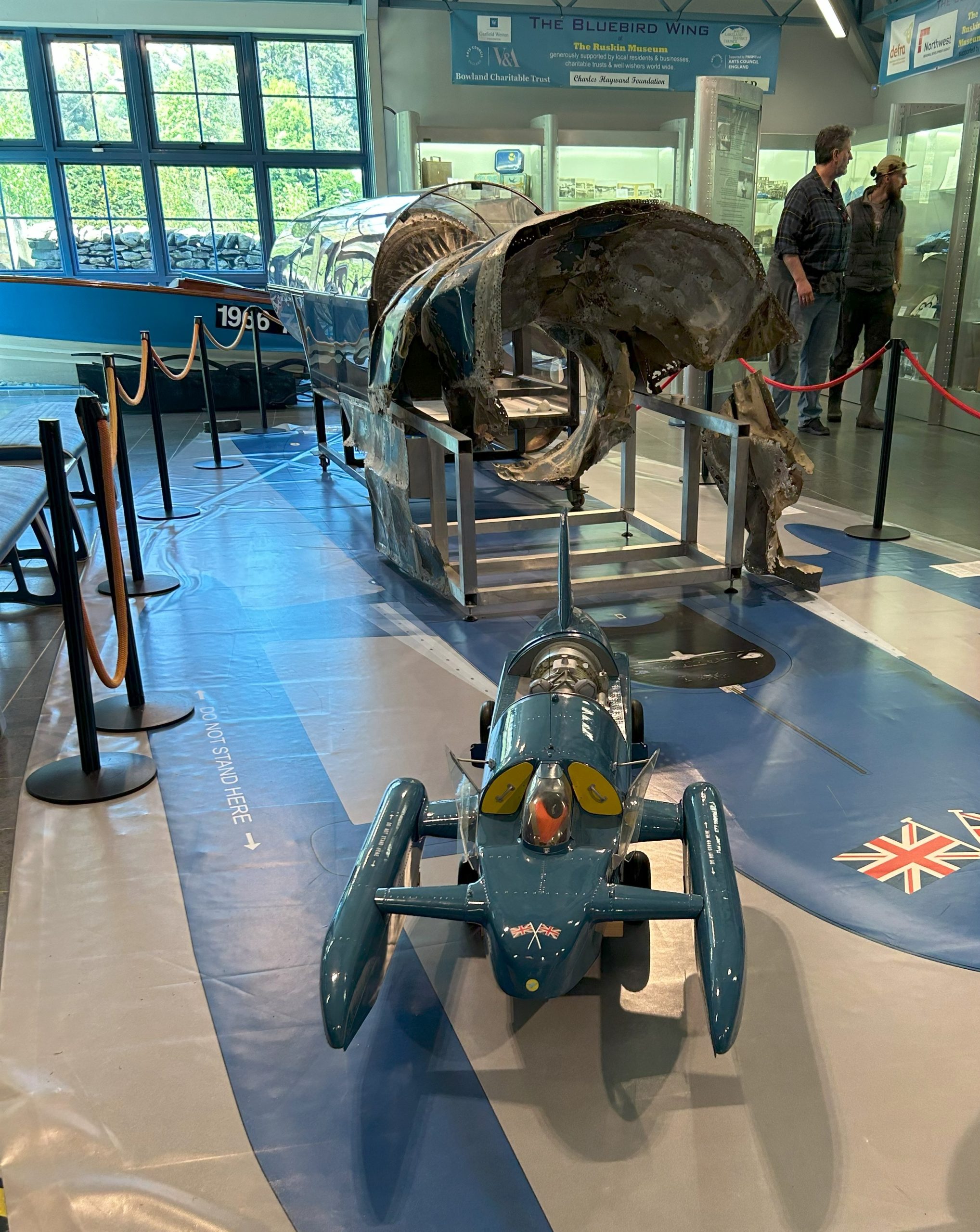
It is such a shame that after all of Donald Campbell’s great achievements on both land and water that the fate of his boat, Bluebird K7 will most likely end up in the courts. The Bluebird Project, after having achieved so much in restoring Bluebird K7 back to running order, are now in effect holding the boat to ransom from the Ruskin Museum, who were given the Bluebird by the Campbell family after she was recovered in 2001. I wholeheartedly support their endeavour to recover Bluebird back to the Museum where she belongs. The museum is now raising funds to support this legal case, which I also support 100%. https://gofund.me/4f12d64a.
Having returned from Coniston Water, back to the project. First task is to design and build a frame to hold the main beams rigid during assembly and construction. Like the construction of full size CN7, my build base was built around some sturdy T section aluminium beams attached to some 18mm marine plywood. This would allow accurate positioning of the main beams as these would form the reference point for all other parts.
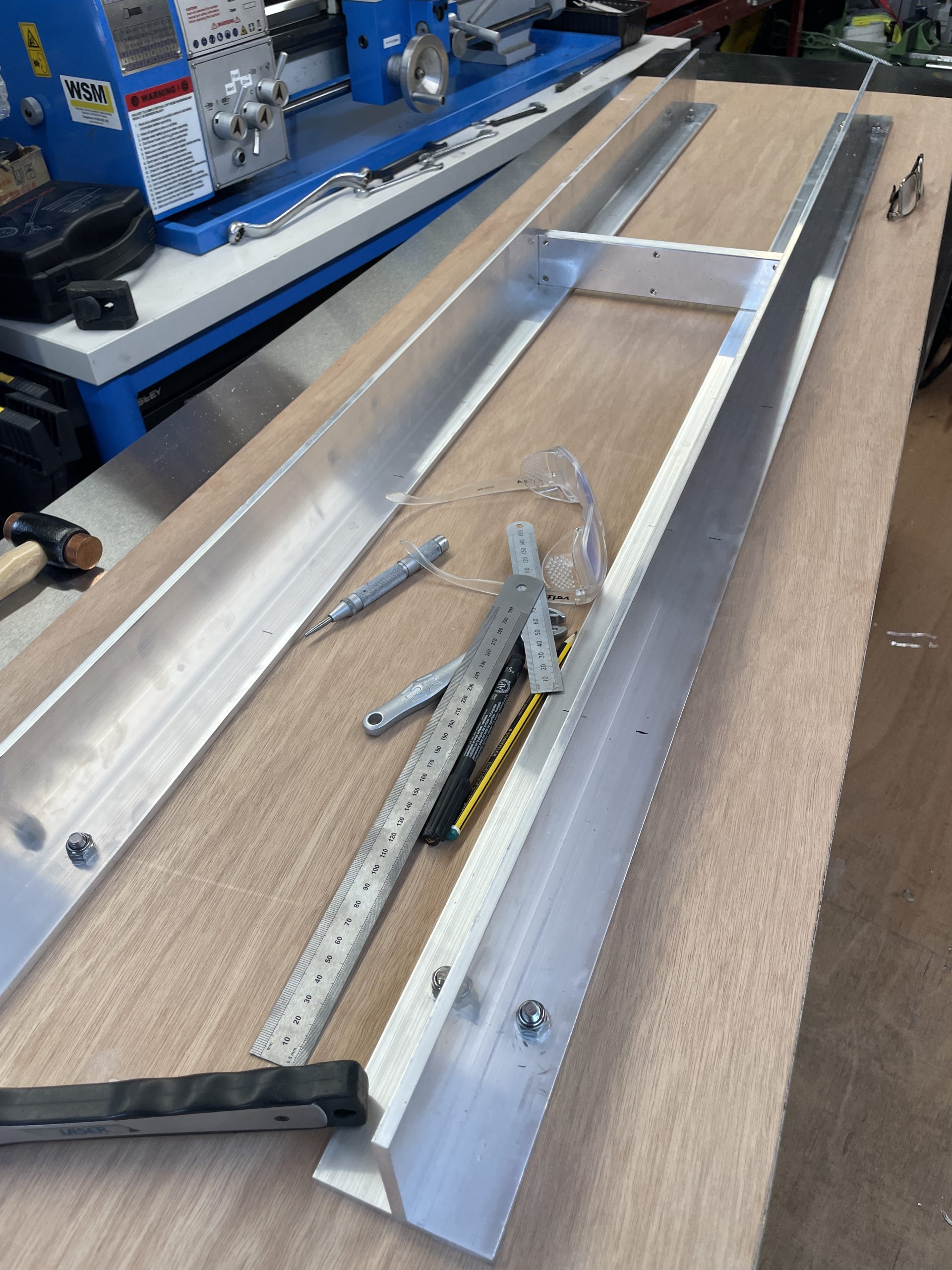
Mounting brackets were 3D printed to attach the main beams to the T section supports. These may be remade in aluminium if additional rigidity is required but for now 3D PLA supports will suffice.
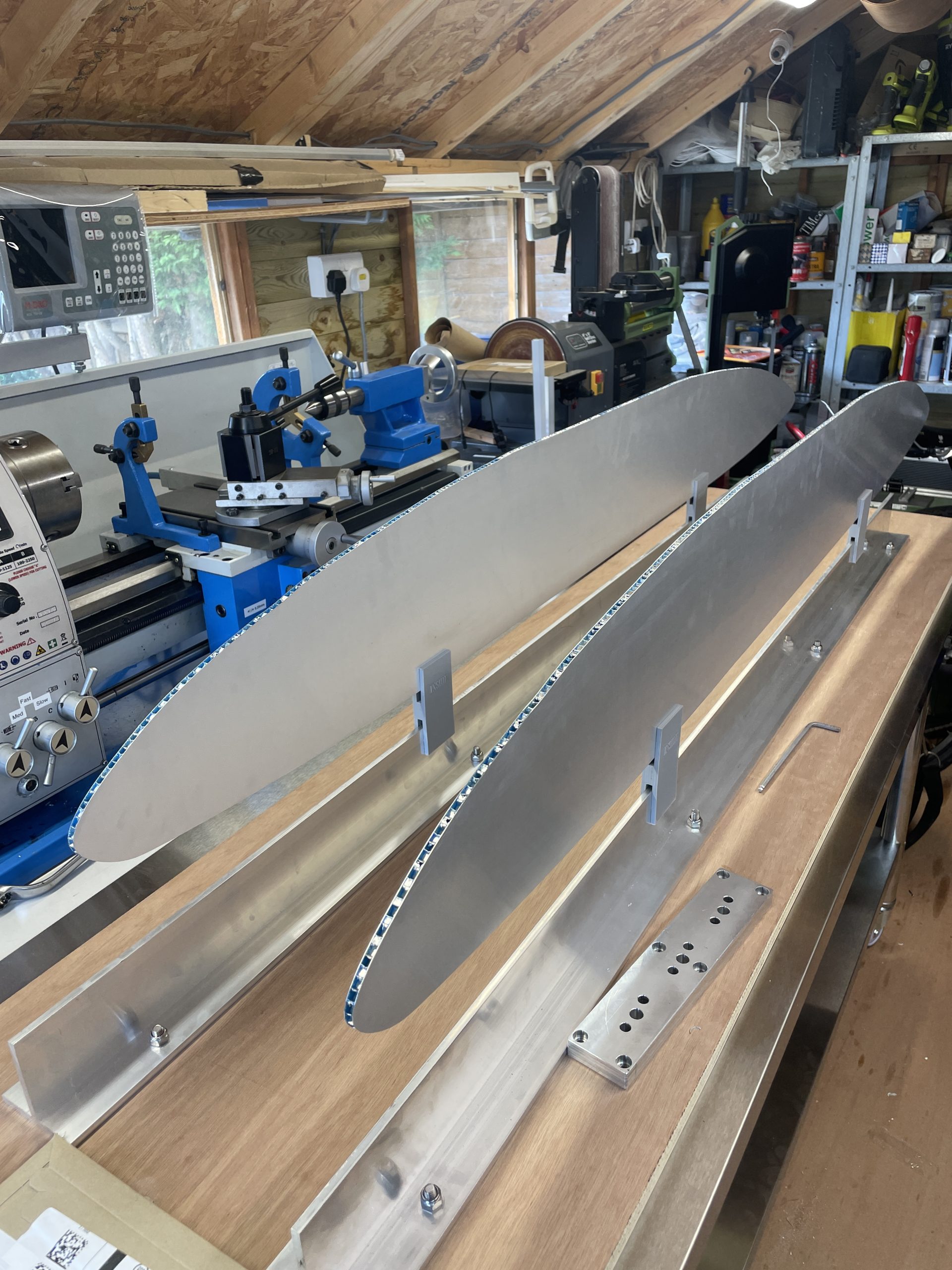
Supports were printed to hold inner beams, these will hold beams at the correct height and offset relative to the main beams.
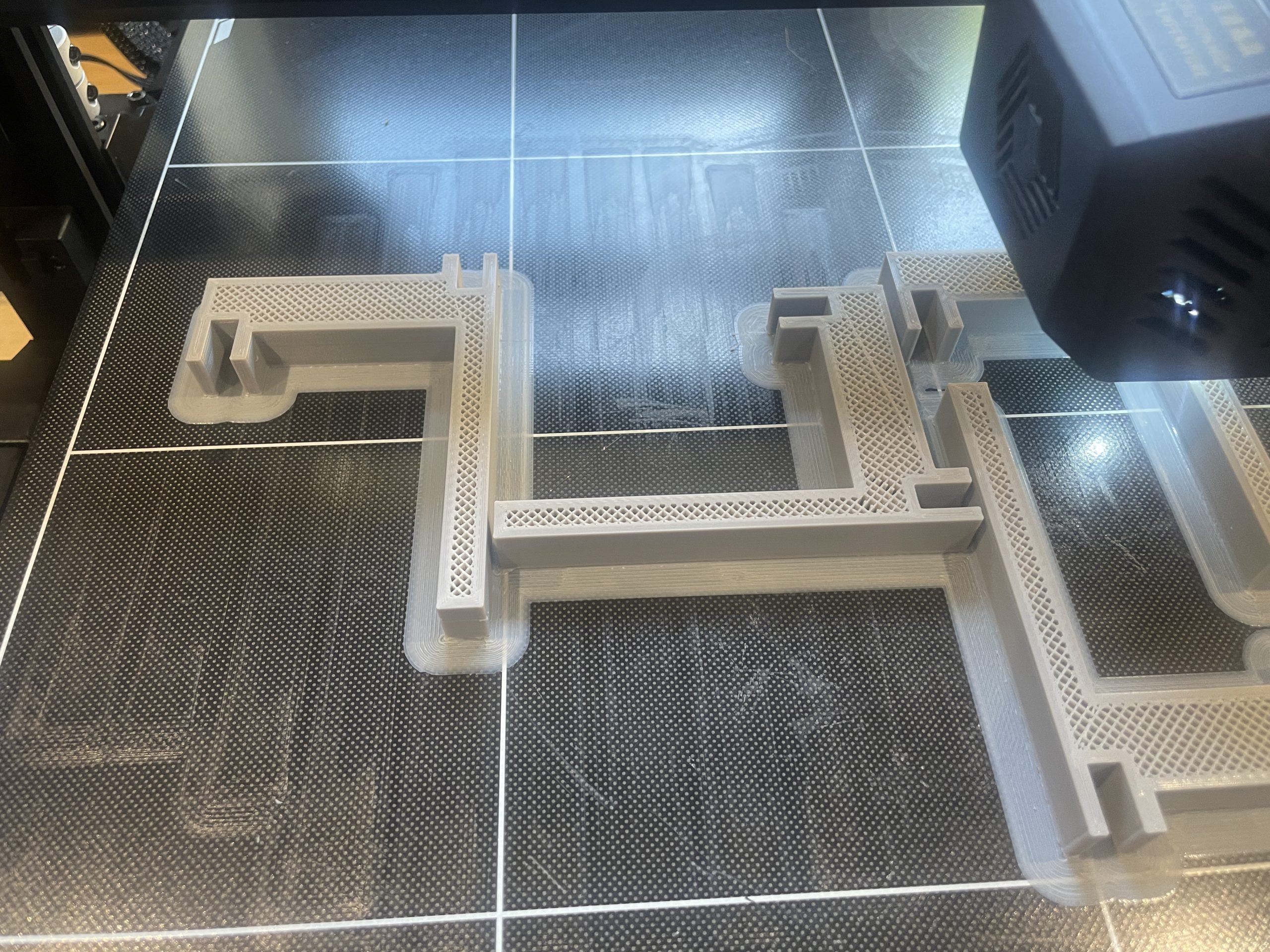
Using the supports, the inner beams can now be mounted inside the main beams with the correct offset. The beams will all now be attached to each other with some temporary ribs which will also be 3D printed, so that layout can be finalised. The inner beams then need to have middle section removed and will be folded out to join directly to the join the main beams. Once everything is temporarily attached internal layout can be finalised, including location of fuel tank(s), LiPo batteries, jet engine, gearboxes etc.
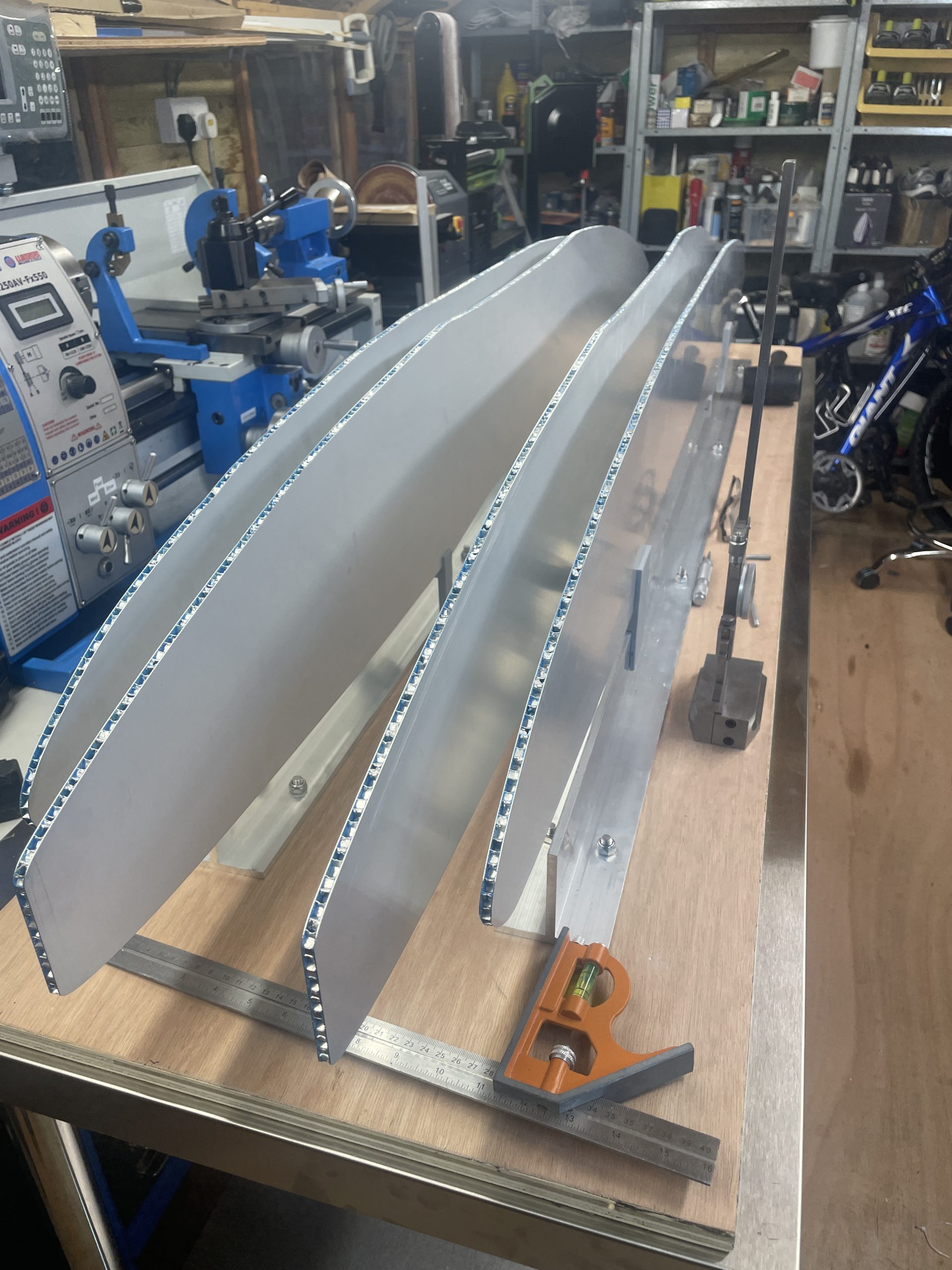
I have been rapidly running out of space in my workshop, which is seriously hampering my ability to work on a large project such as Bluebird CN7. To solve this issue I ordered another shed, which finally arrived, and construction started. The new 12′ x 8′ shed would allow me to move most of the storage which is currently in my main 20′ x 10′ workshop to the new shed. This will allow me to simply use the larger workshop for projects and allow more room to work on things and use the machine tools.
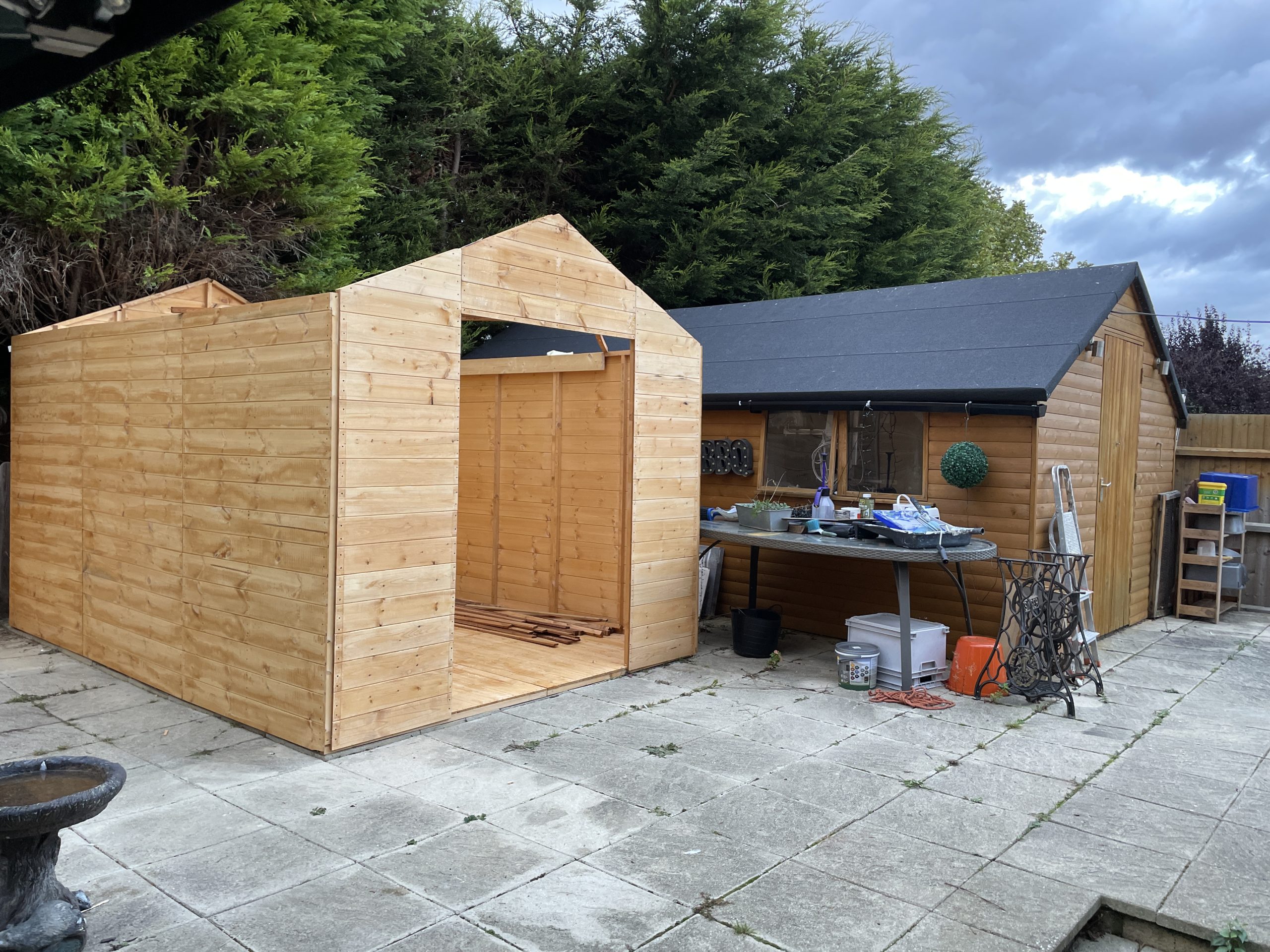
I have been spending a lot of time perfecting the design of CN7’s chassis in CAD so that I can best understand and perfect the construction prior to starting to put everything together. Although the main beams have been accurately set out on the construction frame positioning of the ribs which connect everything together are critical to form a perfect base to lay the aluminium skin over.
I had always intended to build all the supporting structure in aluminium but having considered the complexity of the 3D chamfering on the edge of each rib which will form the profile for the aluminium skin I have been experimenting with 3D printing the ribs in PLA / PETG. This will allow me to exactly create the correct profile and chamfer for the skin to fit exactly.
This may also allow me to 3D print holes directly into each rib for skin attachment rather than having to create overly complex angled brackets to be attached to each rib although this design strategy may also change. The main beams will remain as currently laid out in composite aluminium to provide a strong and rigid frame.
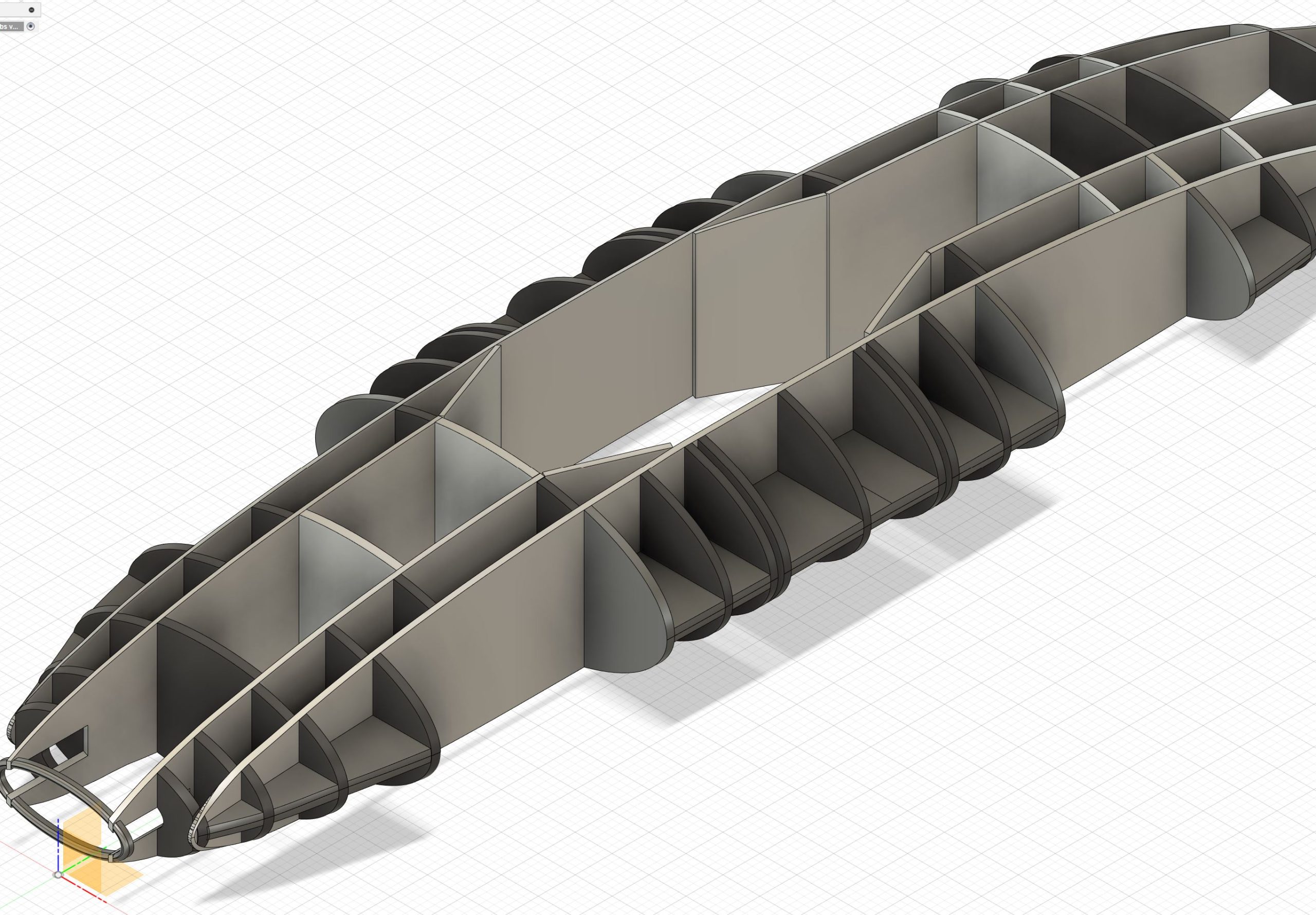
Next Update: October 2023