June 2025
7th July 2025
It has been a very long time since my last update to the website, but I have still been busy with the Bluebird CN7 project.
I have spent many hundreds of hours on CAD refining my design. My intention is to have everything designed on CAD and be certain of functionality of each component prior to starting manufacture or purchase of additional components.
The design for the drivetrain has been finalised, in the end I have opted for a simple belt drive to enable all four wheels to be driven. I did explore many other options but I decided to go with the simplest option.
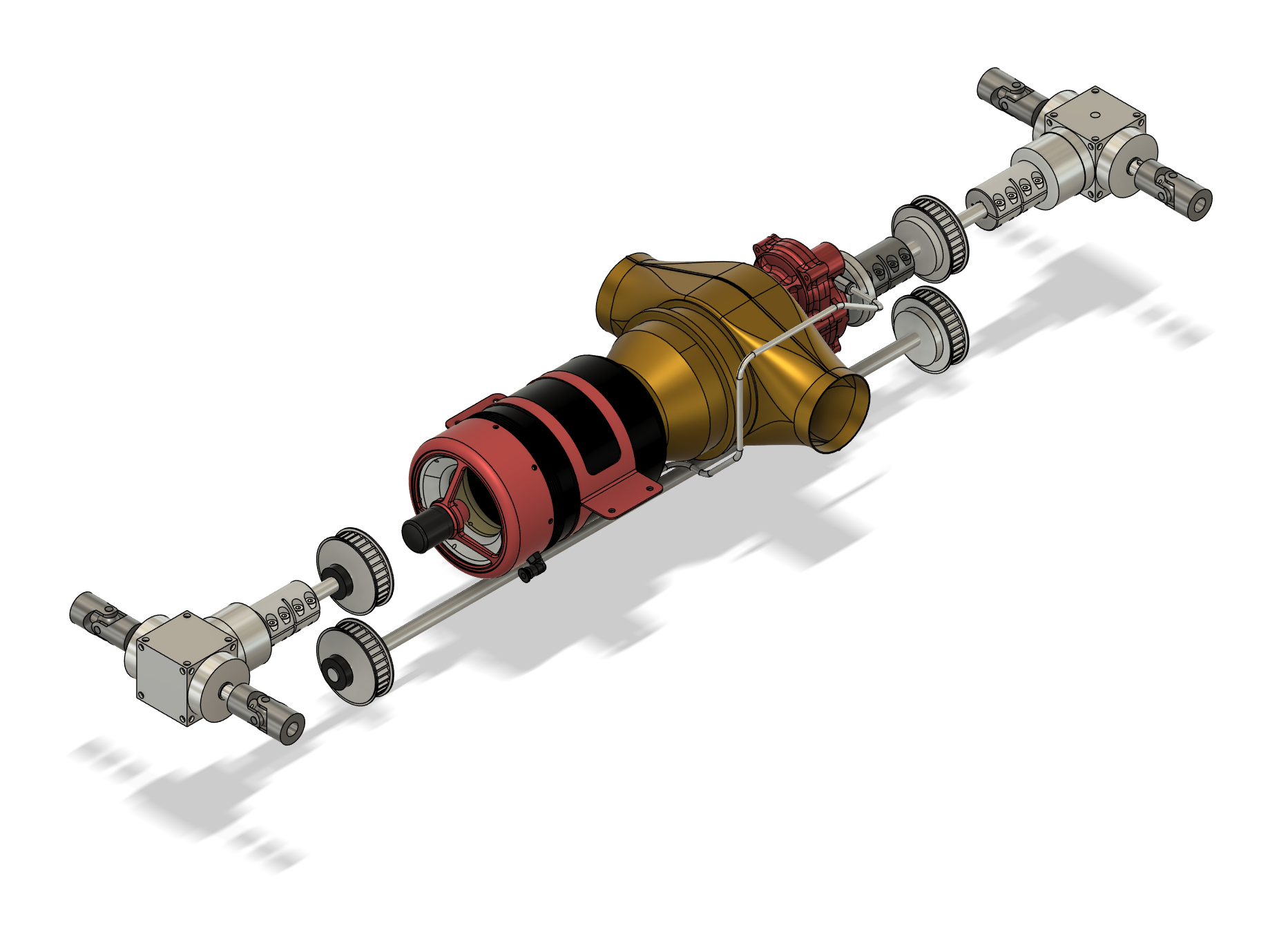
Most components of the drivetrain are commercially available items with only a few parts requiring special machining or custom manufacturing.
The gearboxes I have had for some time and these are commercial spiral bevel gearboxes used in industrial applications. The model is only really designed for straight line use and even though the front wheels have steering, the steering angle will only probable be a few degrees so I decided that differentials would not be required in this case.
The turbine, as mentioned in previous pages will be a Kingtech K-100TPG4+ designed for use in model turboprop aircraft, and has the following performance which should be more than adequate to drive the model. Kingtech very kindly sent me a CAD drawing of the K100-TPG4+ which helped significantly with my design.
- Weight: 3.5kg
- Maximum Turbine RPM: up to 135,000
- Power:13KW @ 6200 RPM (gearbox output)
- Fuel consumption: 360g / min
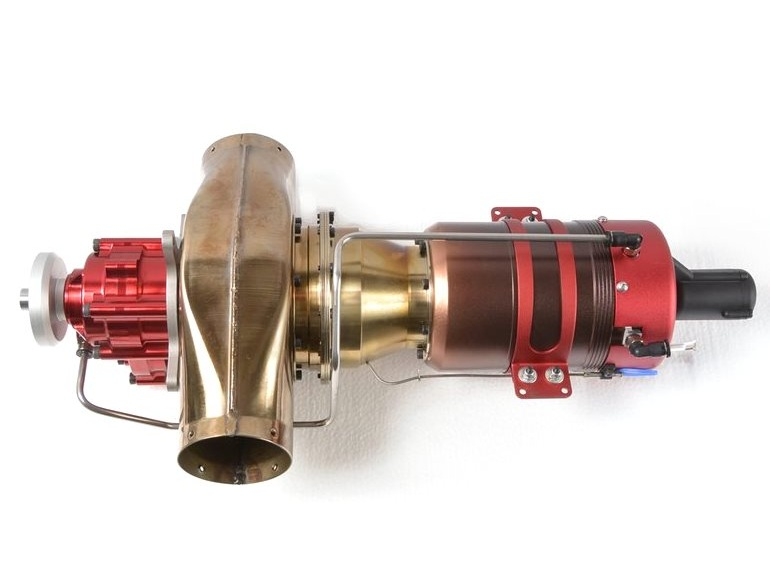
All the pulleys, belts and couplings are commercially available, only the driveshaft will need some machining for keyways etc.
Next part of the drivetrain to design was the suspension, which was to be modelled as closely as possible to the suspension fitted to the original CN7.
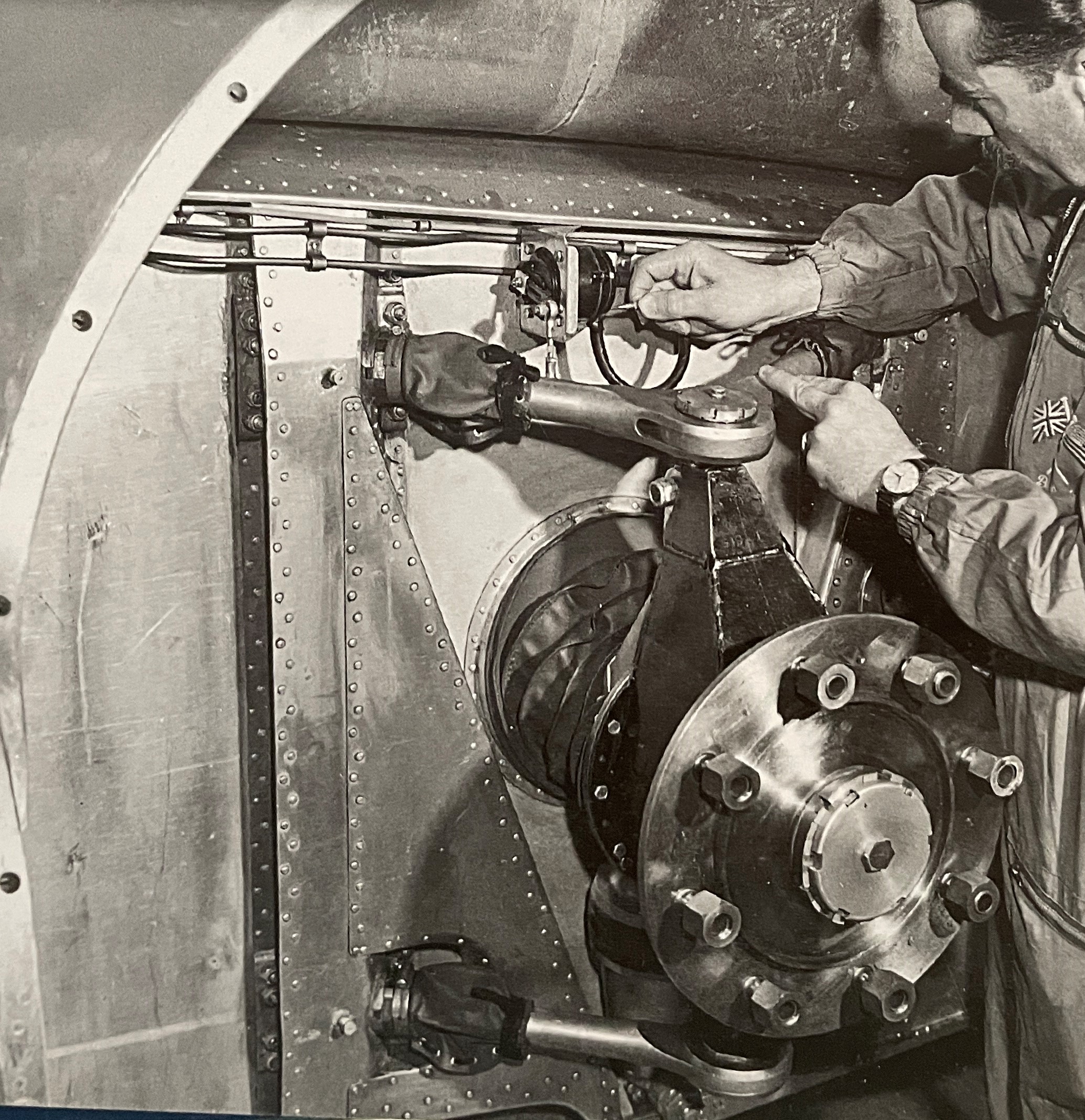
I tried to use as many commercially available parts are possible although a great many parts would need to designed and made from scratch including the following.
- Knuckle
- Wheel Hub
- Control Arms
- Strut
- Mount
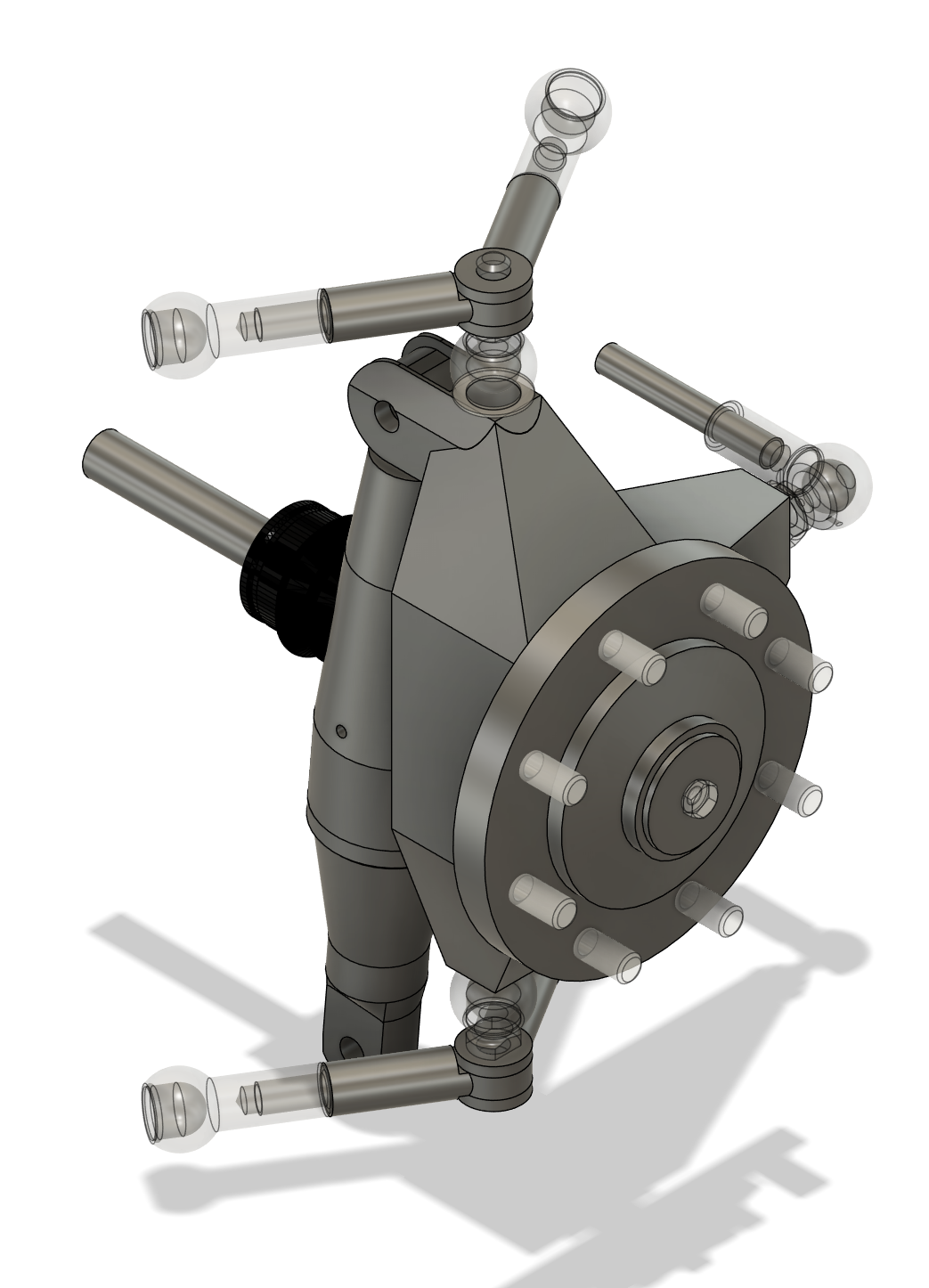
I also wanted to design the strut with working suspension and damping so this needed a considerable amount of thought and design refinement. The strut unusually in this case is under tension rather than compression.
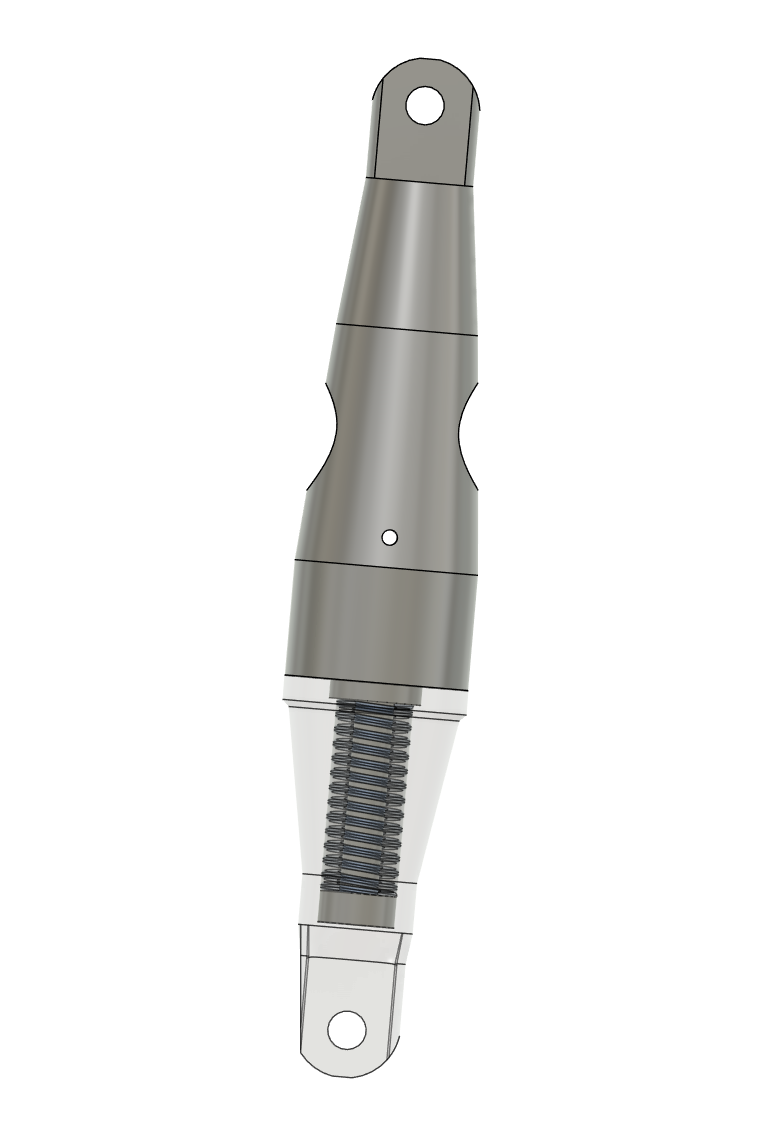
The model would also require a custom exhaust. It was clear early on that the existing exhaust outlets on the Kingtech K-100TPG4+ would need to modified as in their present state they were far too wide and would not allow room for exhaust gasses to be fed out of the rear facing exhaust.
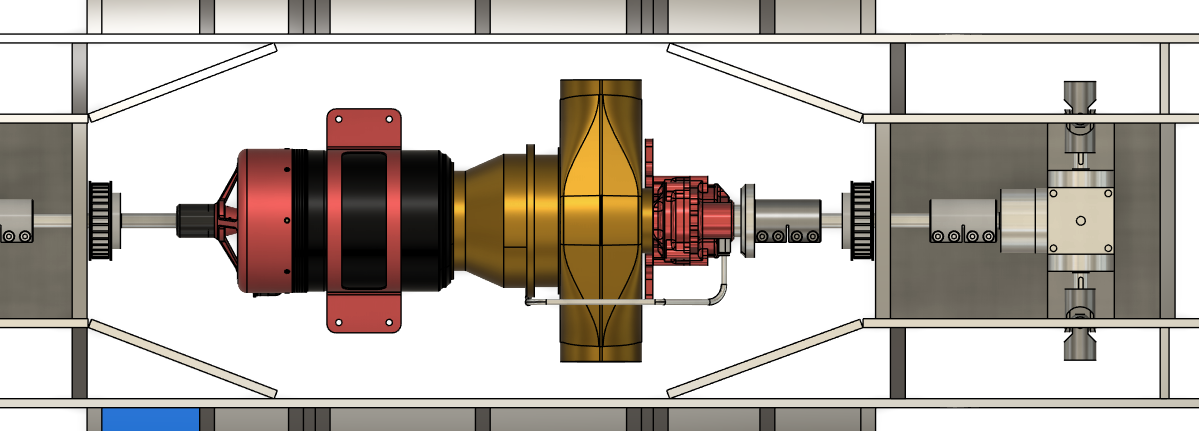
Again a big thanks again to Kingtech as without having the CAD drawings design of this and working out exactly how the existing exhaust would need to be modified would have been almost impossible. I settled on a design that would require minimal cutting of the original exhaust manifolds. I decided on a simple 45 degree cut of the existing exhaust would allow enough space for some custom manifolds connecting to the twin exhausts on each side. Again, as with all of these tasks a lot of learning of CAD techniques was required.
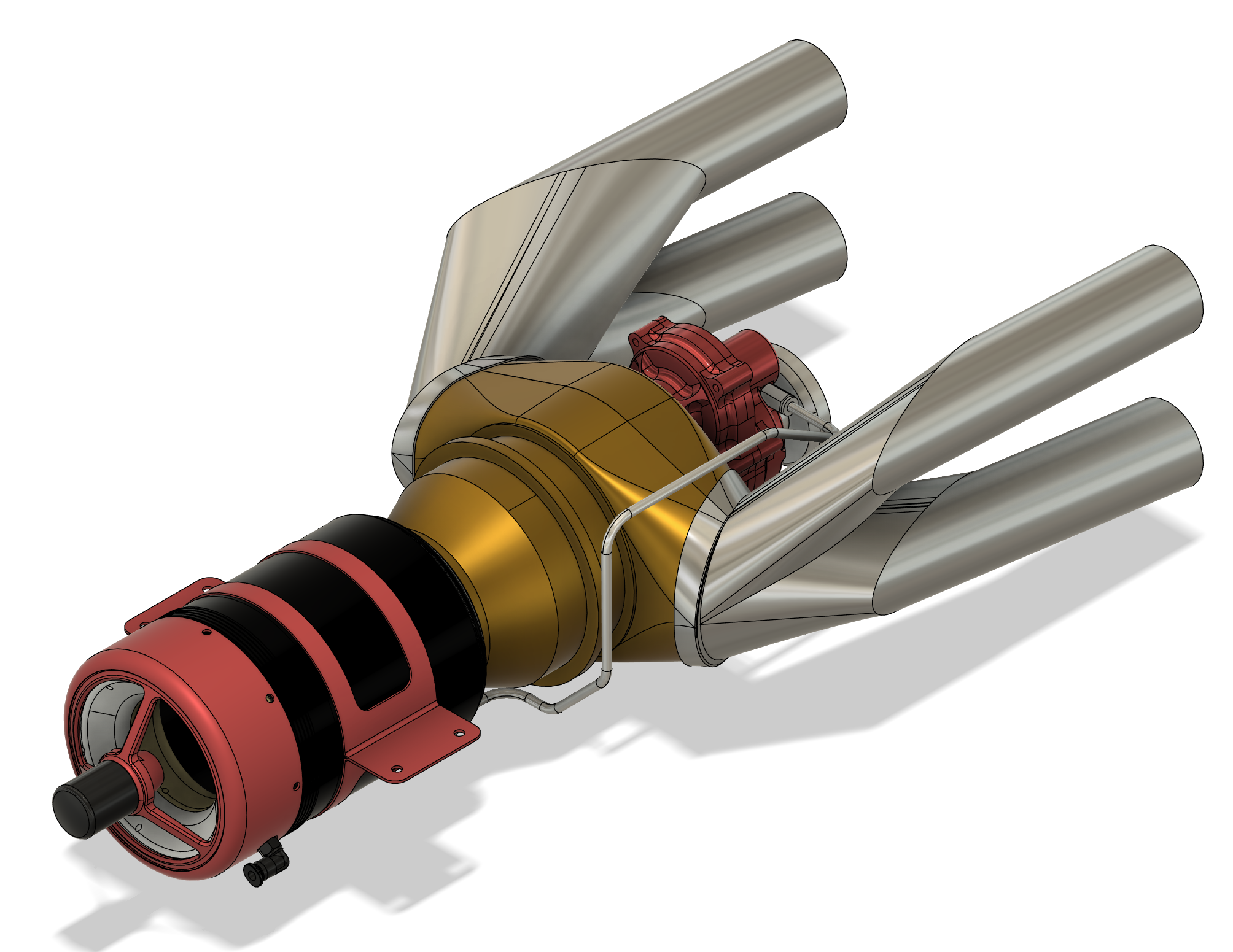
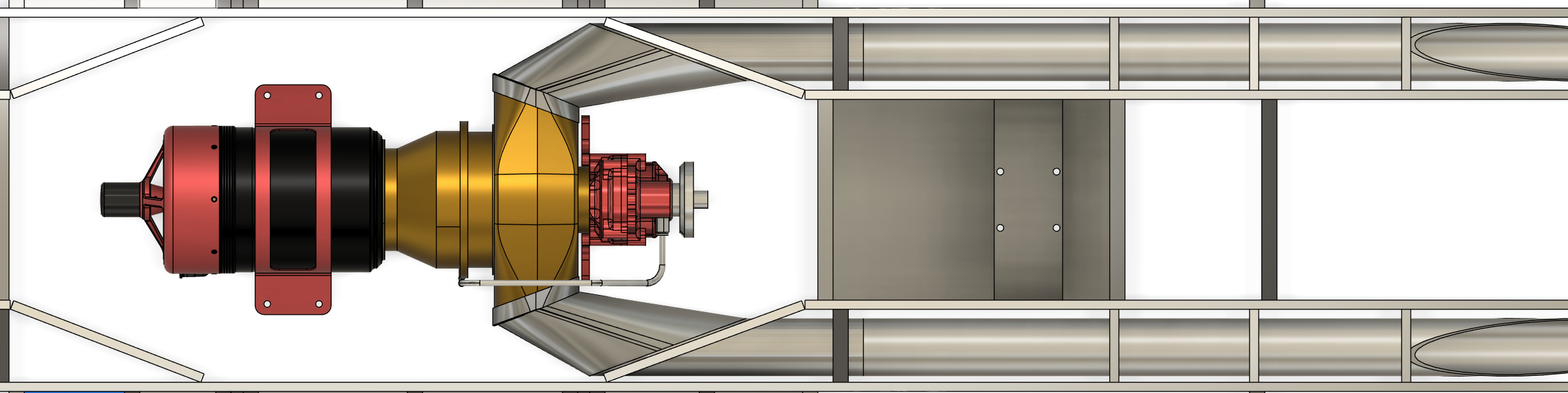
The manifolds will be 3D printed in Stainless Steel using DMLS (Direct Metal Laser Sintering) which is a 3D printing technology that uses a high-powered laser to fuse powdered metal into a desired 3D shape. The exhaust tips will be commercially available 38mm Stainless Steel exhaust tubing.